Here we will introduce MYIR's battery management system (BMS) solution based on MYC-YA157C CPU Module which is a compact ST STM32MP1 powered System-on Module (SoM) targeting applications like industrial control, consumer electronics, smart home, medical and more other energy-efficient applications which require rich performance and low power.
BMS stands for Battery Management System. It is a device to monitor the state of energy storage batteries, mainly for intelligent management and maintenance of each battery unit, preventing the battery from overcharging or over-discharging, extending the service life of the battery and monitoring the state of the battery.
Battery energy storage system consists of battery packs, Power Conversion System (PCS), Energy Management System (EMS), Battery Management System (BMS) and other electrical equipment. Battery packs store electricity; PCS controls the charging and discharging process of the battery pack for AC/DC conversion; EMS for data acquisition, network monitoring and energy scheduling; BMS monitors the running status of each battery in the battery storage unit to ensure the safe operation of the battery storage unit.
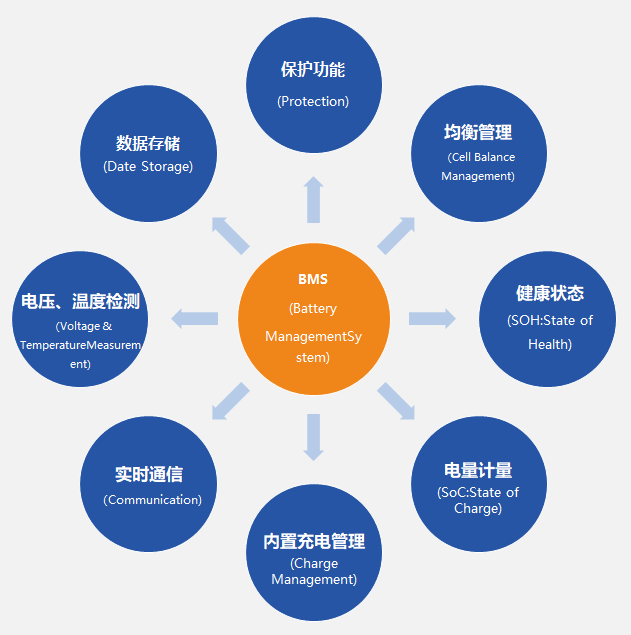
As one of the core subsystems of battery energy storage system, BMS is responsible for monitoring the running state of each battery in the energy storage unit to ensure the safe and reliable operation. BMS can be applied to real-time monitoring and acquisition of status parameters of energy storage batteries (including but not limited to voltage of single battery, temperature of battery pole, current of battery loop, terminal voltage of battery pack, insulation resistance of battery system, etc.), and carry out necessary analysis and calculation of relevant status parameters to obtain more system status evaluation parameters. And according to the specific protection control strategy to achieve effective control of the energy storage battery body to ensure the safe and reliable operation of the whole unit. At the same time, BMS can exchange information with other external devices (PCS, EMS, fire fighting system, etc.) through its own communication interface and analog / digital input interface, forming linkage control of subsystems within the whole energy storage power station, ensuring safe, reliable and efficient operation of the power station.
Due to the large scale of battery packs, most of the energy storage BMS has a three-layer architecture, and there is a total control layer on the basis of slave control and master control.
-
Slave Control: battery module unit (BMU) collects information about a battery, such as the voltage and temperature, calculates and analyzes the SOC and SOH of a battery, balances the SOC and SOH of a battery, and sends the abnormal information to the battery cluster unit (BCU) through CAN communication.
-
Master Control: battery cluster unit (BCU) is used to collect battery information uploaded by the BMU, collect battery packs’ voltage, temperature, charging and discharging current and total voltage, detect battery leakage, and power off protection if the status is abnormal. Calculate and analyze the SOC and SOH of the battery packs, and upload all the information to the battery array unit (BAU) through CAN communication.
-
Total Control: battery array unit (BAU) centrally manages batteries in an energy storage station. Connect each BCU downward to collect all kinds of information uploaded by BCU; Exchange information with the EMS, upload collected battery information over the Ethernet and receive battery operating parameters from the EMS; Communicate with the PCS over CAN or RS485 port, BMS sends the battery status and abnormal information to the PCS, the PCS takes appropriate protection actions after receiving the alarm information from the BMS.
The Battery Array Unit (BAU) adopts MYIR's MYC-YA157C CPU Module which is based on STM32MP1 processor and features dual Arm Cortex-A7 and 209MHz Cortex-M4 cores, supporting one Gigabit Ethernet, two CAN ports and eight UART ports, so that the device can communicate with Battery Cluster Unit (BCU), Power Conversion System (PCS) and Energy Management System (EMS). It features as below:
- Mass storage design and supports system long-term data storage;
- Rich interfaces, HD touch screen display is supported and can be used for local monitoring and energy management;
- Supports Gigabit Ethernet, RS232, RS485 and more other data communication interfaces so that it can be used in various scenarios to meet different requriements;
- Supports WiFi for wireless communication to bring faster response and meet the construction needs of IoT.
Items
|
Features
|
CPU
|
STM32MP157AAC3, TFBGA361, 12×12mm
|
Power Supply
|
Discrete Power Supply
|
DDR3
|
512MB by default (supports up to 1GB)
|
Nand Flash
|
alternative design with eMMC, supporting 256MB / 512MB /1GB Nand Flash
|
eMMC
|
4GB by default (supports up to 64GB)
|
Ethernet
|
On-board Gigabit Ethernet PHY
|
Expand IO Connector
|
1.0mm pitch 164-pin Stamp Hole Expansion Interface
|
Working Temperature
|
0~70 Celsius (commercial grade) or -40~85 Celsius (industrial grade)
|
Dimensions
|
43mm*45mm
|
PCB
|
8-layer design
|
MYC-YA157C CPU Module
MYD-YA157C Development Board
|